
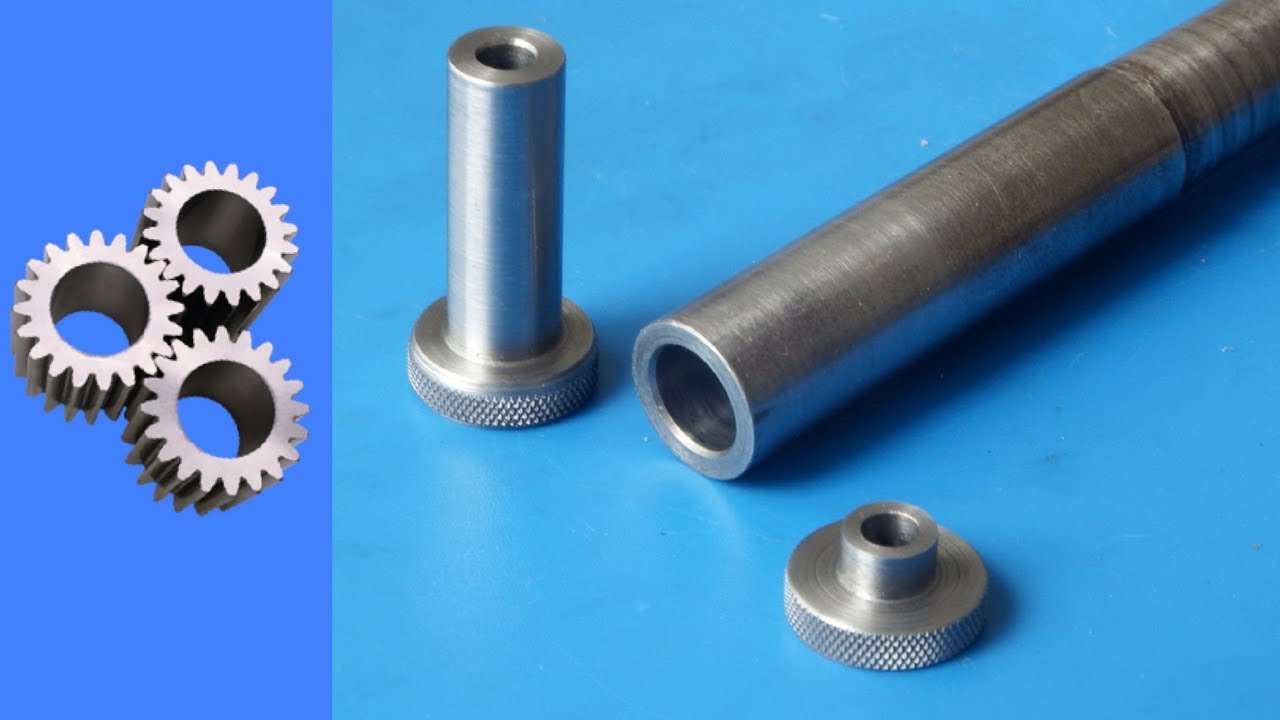
For internal taps with reinforced shank you have to pay attention to the cutting depth, you could hit the workpiece with the reinforced shank. This is suitable for long through holes or blind holes. In contrast to the reinforced shaft, the overflow shaft has the same diameter throughout. Spiral fluted taps promote the removal of chips, especially at high speeds. They are responsible for how the chip flows and in which direction it is removed (important for blind holes). The flute profile can be straight or spiral. Which pitch and which flank angle you need is already determined by the type of thread. The teeth on the thread profile take over the actual cutting process. Hole size and condition can cause many problems with tapping, which are too often wrongly blamed on a tool. I cut tap on the lathe (radially) with rigid ER25 (standard collets), 3-4 coolant (semi-synthetic), 2800 metric M5 blind holes before I toss the tap. Often custom-sized drills are needed to get the best tool life out of roll form taps as the hole size range is very small. Machine taps with flush and reinforced shank are usually manufactured as long version, hand taps as short version. Using this formula you can calculate that a ½-in.-13 UNC thread requires a hole size of 0.466 to 0.469 in. Let us have a look at the DIN standard 2184-2, where the dimensions for taps are defined as long version and for short version. The more threads the internal tap has, the better the centering in the workpiece and less force is applied on the drill. Actually the technically correct name is short machine tap, form A. With the flat head shape you cut into blind holes as well as through holes.
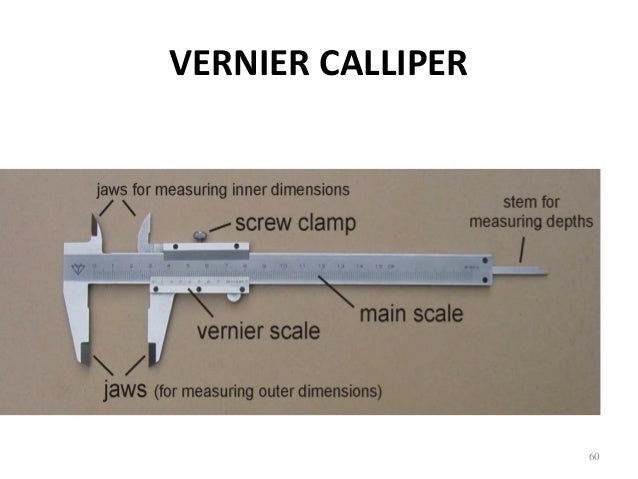
With the pointed head shape you should only cut into a through hole. This makes your circle of possible internal taps extremely small. However, the spiral point tap has the cutting face of the first few threads cut at a pre-determined angle relative to the taps axis angle to force the.
#FORM TAPS VS CUT TAPS ISO#
Threads are standardized according to an ISO norm. In the table we compare the features and their influences on the selection of the suitable internal tap. With internal taps made of high speed steel HSSE-Co 5 you can cut e.g. The required tool steel also depends on the application. In case of hard materials, a longer point cut is advantageous because less force is applied to the tap. Which material will you cut into (application)? Which hole the tap is suitable for is usually written on the packaging.ĥ. Here you decide how many threads you need and in which direction the chip should be removed from the hole. Your thread must also be cut in the same direction.Ĥ.
#FORM TAPS VS CUT TAPS FULL#
thread chamfer remove more material to eventually create a full thread form. Look at the screw or the counterpart to be screwed in. threads are cut by the cutting chamfer portion of the tap during rotation. If you want to drill a lot of threads, you should reach for the machine tap.ģ. Cut taps form threads by cutting the material, creating chips that can clog flutes or collect in blind holes. If you do not have much time, you should use a single-cut tap. Good chip evacuation minimizes thread damage and prevents tap breakage.When choosing the right tap, you must first answer the following questions: Bounce to content text.skipToContent text. The spiral grooves transport the chips out of the drill hole upwards, which prevents the chips from clogging the grooves. Cutting taps and forming taps erzeugung threads that are interchangeable also gage identically, but those are the only similarities between the couple. Taps with right-hand spiral grooves are particularly suitable for blind holes. The chips are removed in the cutting direction. The chip removal of these tap types takes place below the hole. Taps with left-hand spiral grooves are suitable for through holes. Taps with straight flutes are not suitable for deep threads as there is hardly any chip evacuation.ĭetailed view: Tap grooves (spiral groove) of a machine tapĪ distinction is made between taps with left-hand twisted and right-hand twisted spiral grooves: Left-hand spiral grooves on taps Straight fluted taps can have the form A, C, D or E. They are suitable for both through and blind holes. Universally applicable, mainly for short-chipping steel and cast iron, they form the basis of the taps. Taps with straight groove are the most commonly used taps. I am not overly experienced with roll tapping (for whatever reason I have used cut taps for most of my career) so need a little advice. All flute shapes can be found on both cut-in taps and machine taps.ĭifferent tap grooves: Spiral groove, straight fluted with peel point and straight fluted These taps come in 3 different lead amounts: 1.5P (Bottom), 2.5P(Mod Bottom), and 4.5P (Plug). In hand tap sets, all taps are straight fluted. A flute can have different shapes designed for its use, which can cause the material removed to be ejected in a different way. A groove on taps is required to make room for material removal during tapping.
